If you’re a business that manufactures products, it’s necessary to calculate your raw materials inventory. This is essential for tracking quantities and costs and helps maintain a smooth production process. Here’s everything you need to calculate your raw materials inventory and why you should consistently monitor your inventory levels.
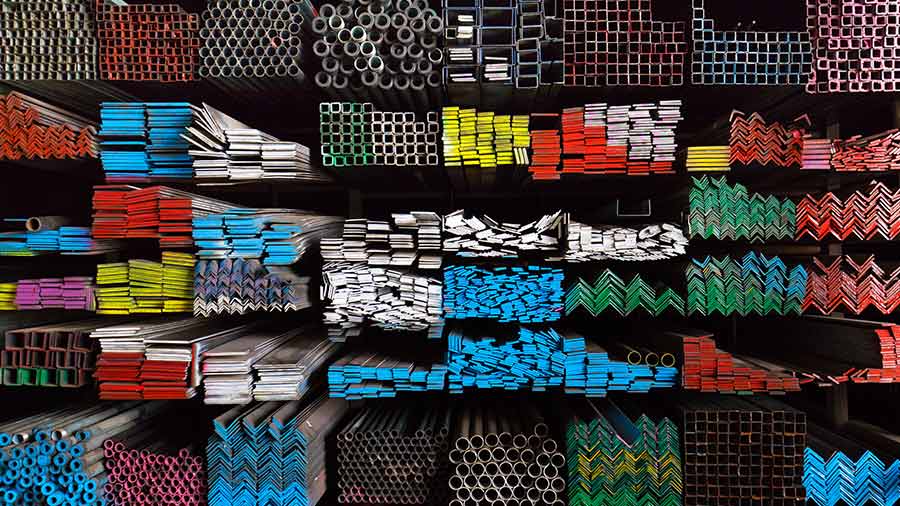
What is Raw Materials Inventory and How to Calculate It
What is Raw Materials Inventory?
A raw materials inventory consists of unprocessed materials gained from suppliers before using them during the production process. Typically, raw materials inventory includes items like:
- basic commodities (e.g., metals, minerals, oil, gas, wood, and agricultural products)
- components (e.g., resistors, capacitors, integrated circuits)
- Chemicals
- Fabrics and textiles
- Packaging materials
Why Should Small Businesses Calculate Raw Materials Inventory?
Maintaining raw materials inventory ensures a smooth production process, meeting customer demand promptly and reducing lead times.
To effectively manage raw materials inventory, you need to track quantities, costs, reorder points, and supplier information.
This management helps with planning production schedules, managing procurement activities, and optimising inventory levels to minimise holding costs while avoiding stockouts. Many companies, including those in the manufacturing, construction, and food and beverages industries, will need to track their raw materials regularly.
How to Use QuickBooks Raw Material Calculator
Our QuickBooks raw material calculator will automatically work out your beginning raw materials inventory number. You simply need to input your cost of goods sold (COGS) and your ending raw materials inventory minus your raw materials purchased.
Raw Materials Inventory Formula
The raw materials inventory formula is simple to use. Use the following formula:
Beginning Raw Materials Inventory = (COGS + Ending Raw Materials Inventory) – Raw Materials Inventory Purchases
Let’s look at the following example.
Say you have 100 units of Raw Material A, which cost $10 per unit, and 200 units of Raw Material B, which cost $15 per unit.
Total Cost of Raw Material A = 100 units × $10 per unit = $1,000
Total Cost of Raw Material B = 200 units × $15 per unit = $3,000
Total Cost of Raw Materials Inventory = $1,000 + $3,000 = $4,000
How to Calculate Raw Materials Inventory
Wondering how to calculate your raw material inventory? It’s a straightforward process. Here's a step-by-step process on how to calculate raw materials inventory:
- Identify the raw materials by determining the types of raw materials you have in stock. Make a list of the various materials used in your production processes, such as metals, plastics, chemicals, fabrics, or packaging materials.
- Determine the quantity of your raw inventory by counting and recording the quantity of each raw material on hand. You can do this by conducting a physical inventory count (also known as stocktaking) or using digital inventory management systems such as QuickBooks that tracks quantities automatically.
- Assign unit costs by determining the cost per unit for each raw material. This calculation includes the purchase price from suppliers, shipping costs, and any other expenses you pay to acquire the materials.
- Multiply the quantity of each raw material by its respective unit cost to calculate the total cost of each item in inventory. This will give you the value of the raw materials on hand.
- Sum up the values by adding up the total values of all the raw materials to obtain the overall raw materials inventory value. This will represent the total worth of your raw materials currently in stock.
Remember to update your raw materials inventory regularly to reflect any purchases, usage, or changes in quantities. This ensures you make accurate calculations and helps you make data-driven decisions about reordering and managing your inventory effectively.
Manage your Raw Materials Inventory with QuickBooks
As a business, tracking your raw materials inventory is necessary for reducing lead times, and shipping products to customers quickly and effectively. With QuickBooks Inventory Management Software, you can create item records for each raw material in your inventory. It allows you to input key details like item name, description, quantity on hand, unit of measure, and cost per unit. QuickBooks helps you keep an accurate record of your raw material inventory levels and allows you to maintain a centralised database of all your raw materials.
Sign up for a 30-day free trial today, or check our pricing to find out more about how QuickBooks can help you manage your raw materials inventory.
Frequently Asked Questions
Looking for something else?
TAKE A NO-COMMITMENT TEST DRIVE
Your free 30-day trial awaits
Our customers save an average of 9 hours per week with QuickBooks invoicing*
By entering your email, you are agree to our Terms and acknowledge our Privacy Statement.